Although less obvious than carbon emissions from automobiles and power plants, the production of steel is nonetheless a substantial contributor to the global carbon emissions problem. Because of this, there is now a lot of pressure on the steel industry around the world to switch to making “green steel” to help fight the climate catastrophe.
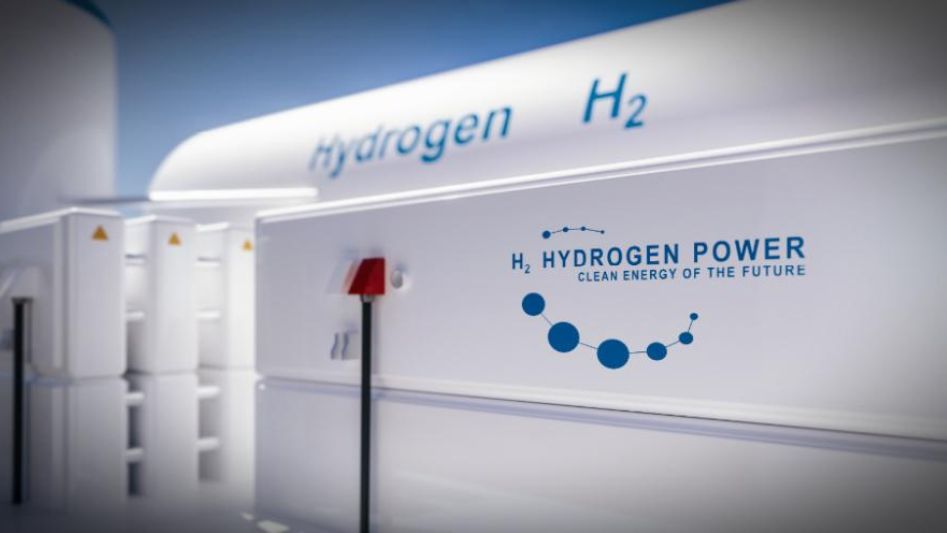
Steel is the metal that is utilized the most in the world and is very necessary for today’s civilization. It is present in every facet of our lives, from automobiles and bridges to aircraft and cruise ships, refrigerators and microwaves, and so on.
Each ton of steel produced by the steel industry equates to 1.85 tons of carbon dioxide emitted into the environment each year. Each year, the steel industry generates almost 2 billion tons of steel. This accounts for approximately 8% of total global carbon emissions.
After being refined and subjected to a series of chemical transformations throughout the manufacturing process, iron, the primary component of steel, as well as trace quantities of carbon, are added. In the more common way of making steel, this process requires a lot of coal.
First, the coal is heated to a high temperature in order to drive out water and other contaminants, which leaves behind a nearly pure form of carbon known as coke. The coke and iron ore are then heated in a blast furnace that is powered by coal and reaches temperatures of three thousand degrees. This is done in order to initiate a chemical process in which oxygen atoms in the ore are dislodged from their bonds with iron atoms. Pig iron is the raw, molten iron that is produced as a byproduct of the reduction process. Steel is made from pig iron as well as the CO2 that is produced during the reduction process. Pig iron is the essential component.
Pig iron, which already has a level of carbon that is excessive for the production of steel, is then transferred to a second furnace known as a basic oxygen furnace, where it is subjected to high-velocity blasts of oxygen that has been cleaned. The carbon content of the iron is reduced by this process, which also results in the production of carbon gas byproducts. At some point, the iron turns into crude steel, which can then be improved to make better steel alloys.
It should come as no surprise that a significant portion of the initiatives under way to cut carbon emissions from steel production involve eradicating coal’s role as a primary source of fuel for furnaces and as a reduction agent. This is because coal, along with the carbon emissions that come from using it, is a key part of the way steel is made in the traditional way.
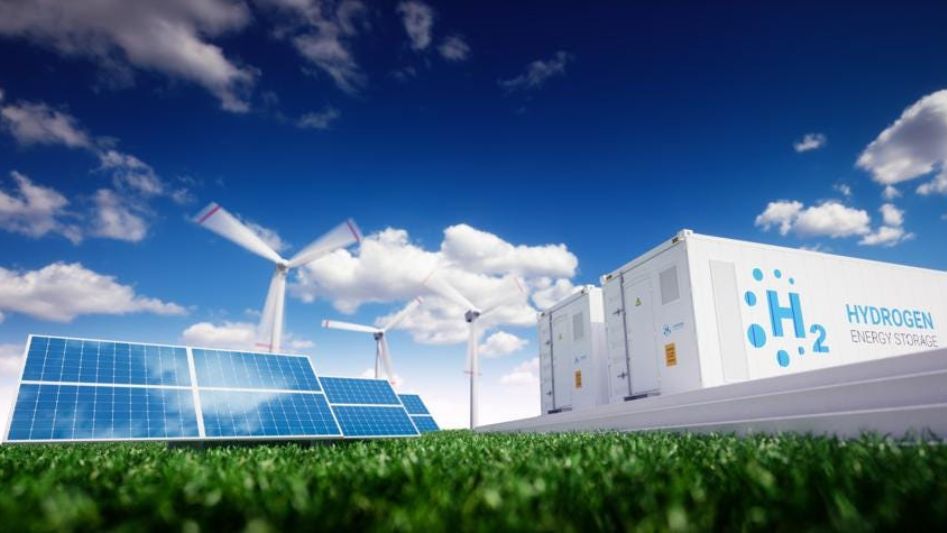
Sweden is home to one of the most prominent initiatives that are now under way to achieve this goal. A project known as HYBRIT (Hydrogen Breakthrough Ironmaking Technology) is currently under way in an effort to decarbonize the entirety of the steel manufacturing process. This project is a collaboration between SSAB, a steelmaker; LKAB, an iron-ore mining company; and Vattenfall, an electrical utility that is owned by the state. In this process, coke is not used; rather, hydrogen gas is used as a reduction agent. This leads to “direct reduction,” which solely results in the production of water as a waste product. The “direct-reduced iron” is then sent into an electric arc furnace, which is a more energy-efficient furnace that melts the iron combined with a small quantity of coal to generate steel. Since carbon is needed to make steel from iron, this process is needed to make steel from iron.
Sadly, this does not completely resolve the issue with the carbon content of steel. Natural gas is the most common source of hydrogen, and the process of extracting hydrogen requires a significant amount of energy, the majority of which originates from fossil fuels. The production of green hydrogen, on the other hand, begins with electrolysis, which is a technique that separates hydrogen from water. Yet, like with all other industrial operations, this too needs energy. A massive quantity of renewable energy would be needed to make the shift to really environmentally friendly steel, which would be made using green hydrogen. Even in that case, direct emissions from iron mining and transportation would still need to be brought under control.
In spite of these obstacles, it is abundantly obvious that the manufacture of steel is moving in the direction of environmentally friendly steel. Seven out of the ten nations that produce the most steel have made at least one investment in a green steel project, and the top five steel-producing businesses each have at least one project in the planning stages.
In addition to the HYBRIT initiative, a number of other businesses and start-ups are doing research and development on innovative, cutting-edge technologies that might help reduce the carbon footprint of steel production. SuSteel, an Austrian company, plans to use hydrogen plasma to reduce iron ore while simultaneously adding just enough carbon to make crude steel. This will eliminate the need for the eclectic arc furnace processing that is now in use. Electricity is used in the process known as molten oxide electrolysis, which is being developed in Boston by a spinoff company of the Massachusetts Institute of Technology (MIT) called Boston Metal. This method reduces iron ore to pure liquid iron that can then be refined.
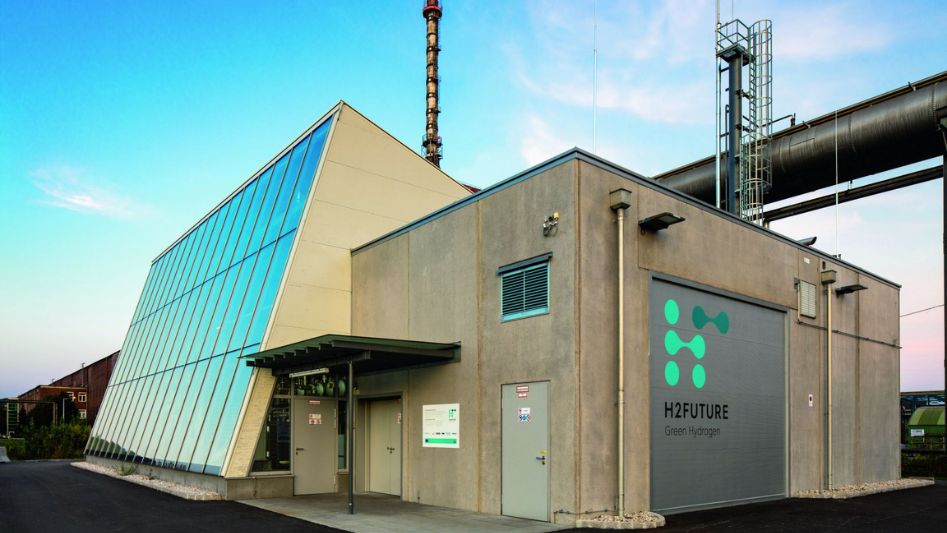
There is no indication that demand for steel will slow down over the course of the next several decades; in fact, some analysts predict that it will almost treble by the year 2050. Even though the production of environmentally friendly steel still has a long way to go before it can be scaled up and become cost-competitive, it is clear that a change at the industrial level is needed to lessen the effects of one of the most important and carbon-intensive commodities.
You May Also Like
WHAT IS AN ESG SCORE AND HOW IS IT CALCULATED?
HOW CO2 COULD BE THE FUTURE OF ENERGY STORAGE?
ESG REPORTING 101: ALL YOU NEED TO KNOW & HOW TO GET STARTED