Researchers believe that if the chemical is made with renewable energy, The Green Ammonia could be used as a clean source for fertilizer, fuel, and heat.
Table Of Content
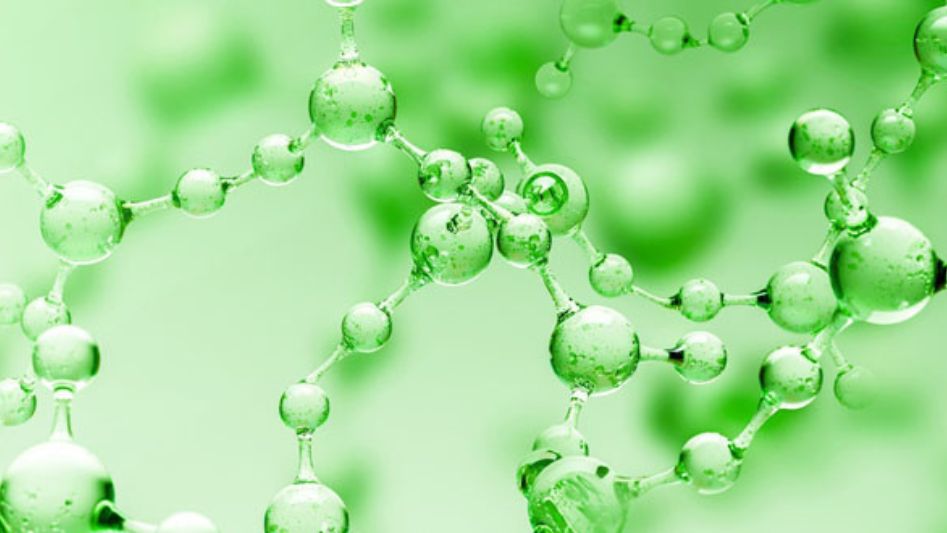
When it is operating at full capacity, a research farm in the state of Minnesota that is covered with wind turbines may brag about having an impressively small carbon impact. The wind provides power to a chemical plant that produces ammonia. This ammonia can not only be spread as fertilizer beneath the turbines, but it can also power an experimental tractor, store energy for use on days when there is no wind, and, in the near future, heat the barns that are used to dry the farmers’ grains. All of this would be impossible without the release of CO2.
Michael Reese, the head of the project at the University of Minnesota, thinks that switching to green ammonia is necessary in order to achieve “deep decarbonization” of agriculture. According to the findings of a study conducted by the university, utilizing “green” ammonia (“green” in the sense that it is produced using renewable energy) as a fertilizer, fuel, and heat source might reduce the carbon footprint of farming by as much as 90 percent for maize and other minor grain crops. Reese identifies it as a transforming statement.
The use of green ammonia is not confined to agricultural settings, according to proponents of this alternative, zero-carbon liquid fuel. They forecast a large new market for green ammonia as a fuel, one that will ultimately surpass the existing enormous (and rising) demand for ammonia as a fertilizer around the globe. According to a report that will be published by the International Energy Agency in 2021, in order to achieve the goal of having zero emissions by 2050, hydrogen-based fuels (including ammonia) will need to make up nearly 30 percent of all transport fuels by 2050. This percentage is practically nonexistent right now. According to the findings of that report, automobiles will soon be powered by batteries, and planes will fly on biofuels; however, the shipping industry, which is currently responsible for 3 percent of global emissions and is working hard to reduce that number as quickly as possible, will continue to rely heavily on ammonia.
In addition, ammonia is one of the leading candidates for storing and delivering energy derived from renewable power plants, making it possible to have access to electricity both when and where it is required. The goal is to generate green ammonia from non-fossil fuel sources using renewable electricity, transport it via pipeline or ship, and then burn it in power plants that have turbines that are specifically designed to operate on ammonia. According to research published in 2020 by the Oxford Institute for Energy Studies, liquid ammonia is difficult to beat for large-scale, long-term energy storage. Although batteries are effective, they are best suited for storing smaller quantities of power for a period of several hours or days. There are governmental plans in place for a number of countries, including Japan, Australia, the Netherlands, and the United Kingdom, to employ green ammonia as a means of storing (and perhaps exporting) their surpluses of renewable energy.
A scientist named Douglas Macfarlane, who works at Monash University in Melbourne, Australia, forecasts that the amount of ammonia produced worldwide will increase by around 100 times over the next several decades.
However, the manufacture of ammonia is not in any way environmentally friendly at this time. The current global production of ammonia amounts to a staggering 175 million tons per year, the vast majority of which is put to use as fertilizer. This massive amount of ammonia is produced through an industrial process that is over a century old, requires a lot of energy, and emits a significant amount of greenhouse gas. This sector is one of the most polluting on the globe since it is responsible for anywhere between 1 and 2 percent of the world’s total carbon emissions.
If ammonia is going to play a role in the global effort to combat climate change, this situation will need to be rectified. It is a significant challenge to ensure that all of this ammonia is clean change, this situation will need to be rectified. It is a significant challenge to ensure that all of this ammonia is clean. The production of the ammonia that will be used to store wind and solar electricity will, of course, make use of the renewable energy that it will store. However, in order to fulfill demands for fuel and fertilizer, much more renewable energy will be required on top of that. Ammonia facilities will need to make changes to their production methods or possibly start from scratch. In addition, the configuration of the engines will need to be altered so that they can operate on the new liquid fuel. Along the way, both producers and consumers will have to overcome obstacles, including the toxicity of ammonia and the possibility that its combustion may generate a greenhouse gas that is even more powerful than CO2.
“It’s not going to happen tomorrow,” adds Macfarlane. “It’s not going to happen overnight.”
There was a time when pure hydrogen (H2) was thought to be the fuel of the future. Hydrogen, on the other hand, has certain drawbacks: in order to exist in liquid form, it must be cooled to cryogenic temperatures of around -250 degrees Celsius; in order to exist in gaseous form, it must be held at high pressure; and in air, hydrogen is explosive. On the other hand, ammonia (NH3) is simple to store as a liquid and nevertheless delivers a powerful punch despite having around half the energy density of conventional fossil fuels. Even though it is poisonous, there is already a massive infrastructure in place across the globe for the production, storage, and transportation of ammonia. Jimmy Faria, a chemical engineer at the University of Twente in the Netherlands who has mapped out ammonia’s benefits, says, “It checks all the boxes.”
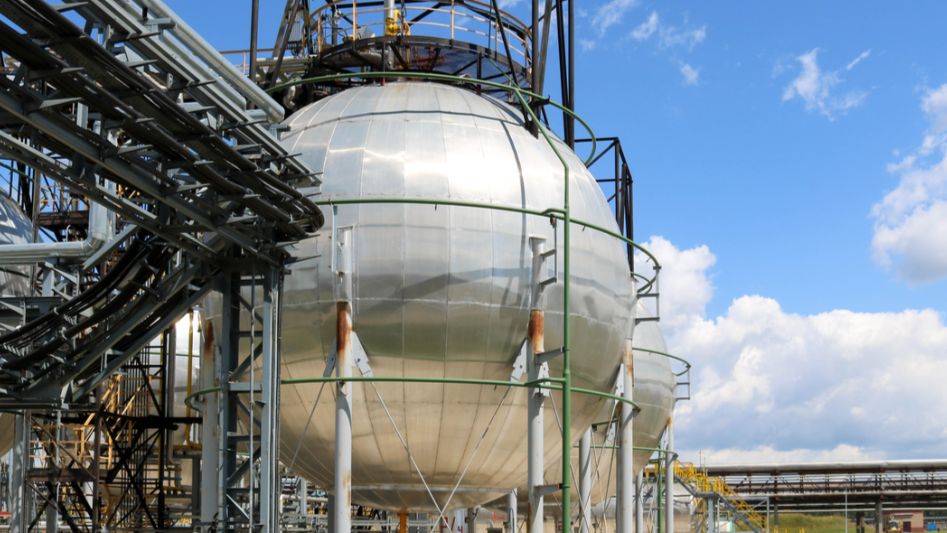
Ammonia is traditionally and inexpensively produced by first removing hydrogen from natural gas using steam, which results in the production of carbon dioxide as a byproduct, and then combining the hydrogen that was removed with nitrogen extracted from the air under high pressure and temperatures in the hundreds of degrees Celsius range. This technique, which is also known as the Haber-Bosch process after the two scientists who won the Nobel Prize and devised it in the early 1900s, generally emits approximately two tons of carbon dioxide into the atmosphere for every ton of useable ammonia that is produced.
Eliminating the use of natural gas and replacing it with the creation of hydrogen via the splitting of water using energy derived from renewable sources is the quickest and easiest option to reduce the emissions that are produced during the manufacturing of ammonia. The remainder of the Haber-Bosch process is carried out in the same way, except now it is fueled by energy generated from renewable sources. When it first opened in 2013, the Minnesota facility, which is situated at the University of Minnesota’s West Central Research and Outreach Center in the town of Morris, was engaged in this activity. Many other commercial initiatives intend to engage in the same activity. According to Macfarlane, “This is a really active area; there is news out every day.” [Citation needed]
Both Britain and Japan have begun operating wind-driven green ammonia facilities as part of a research program since 2018. CF Industries, the company that is now the biggest producer of ammonia in the world, wants to have a flagship green ammonia facility in Donaldsonville, Louisiana, producing 20,000 tons per year by the year 2023. This plant will be located in the United States. Yara’s Pilbara ammonia plant in Australia seeks to generate 3,500 tons of green ammonia per year by the end of 2022, with the goal of increasing production by a factor of 50 by the year 2030. The Saudi Arabian plan for the biggest project now in the works is as follows: A facility that is expected to operate in the year 2025 will have the capacity to produce 1.2 million tons of green ammonia each year. According to Macfarlane, these plants are energy hogs that need specialized wind or solar farms to provide them with the necessary electricity.
In spite of the rush of activity, this represents a small portion of the current annual worldwide output of 175 million tons of ammonia. To increase world output by a factor of 100, it would need the equivalent of 10,000 million-ton plants. According to Faria, there are dangers associated with such an expansion, including the accidental release of ammonia and even the pollution of the environment with highly concentrated salt. The latter is a byproduct of the desalination process that is required to make all of the water into green hydrogen.
According to Faria, a scale-up of this kind is “achievable” with the technology that is now available, but it will be costly. According to the findings of the Oxford study, the cost of producing ammonia using electricity is 73 percent more than the cost of producing ammonia at a large facility in the United States that uses fossil fuels. Faria points out that the cost is very dependent on the price of power in the area and that the market is moving really quickly.
According to Faria, the price of wind and solar energy has decreased “dramatically” over the last seven or so years. It is just a matter of time, according to him, until clean hydrogen is available at prices that are on par with, or even lower than, those of its polluting counterpart. According to chemical engineer Prodromos Daoutidis, who works with Reese at the University of Minnesota, in order to get green ammonia going quickly enough and on a large enough scale, government policies will likely be required to help subsidize green hydrogen and encourage economies of scale. Daoutidis says this. Reese is also involved in the project. Until then, there is a risk that businesses such as shipping that want to utilize ammonia as fuel would wind up utilizing “dirty” ammonia for power, which would merely move emissions from one industry (shipping) to another (electricity), which would be counterproductive (ammonia production).
During this time, advances will also be made in industrial technology. According to Daoutidis, making improvements to the Haber-Bosch system is difficult since it is a well-established and effective technology. However, there is some room for negotiation. The United States Department of Energy has granted Reese and his coworkers ten million dollars to fund the construction of a pilot plant that will test two innovations. These innovations are a new and improved catalyst as well as an absorption salt that will be used to pull the ammonia out at the end of the process. They are hopeful that the reduction in capital costs and the need for high pressure will result from these considerations.
Macfarlane is putting his money on even more significant shifts. He sees an altogether new method of producing ammonia as opposed to just altering the source of the hydrogen or tinkering with the particulars of the process. The goal is to use an electrochemical cell to manufacture ammonia directly without first needing to produce hydrogen, a necessary component of the reaction. After many years of labor, this so-called “generation 3” technology has proved to be a chemical challenge that is difficult to solve. According to Faria, “This is still a really tough task.” Macfarlane is the founder of a new firm called Jupiter Ionics, which is working on a cell that will accomplish this goal by using an electrolyte that is similar to the one used in lithium batteries.
According to Macfarlane, an electrochemical device the size of a shipping container might produce one metric ton per day of green ammonia. These systems, in contrast to those at Haber Bosch facilities, would be compact and simple conventional activate and deactivate. According to Faria, this might prove to be a game changer for areas such as distant communities in Africa or, for example, the wind-rich Caribbean island of Curacao. In these locations, it is difficult or costly to import gasoline, and fertilizers are expensive. Produce produced locally might provide sustenance and energy for outlying farms and communities. However, a significant number of chemists share Macfarlane’s skepticism that this can be accomplished on a commercial scale anytime soon. Daoutidis believes that the technologies being discussed have a great deal of potential, but that their development is still in the early stages. “It’s a question mark.”
After the production of green ammonia has been completed, further infrastructure will be required to make use of the substance, such as the ability to burn it in a combustion engine to power a ship or to drive the turbines of a power plant.
Ammonia-fueled combustion engines have been present since the 1800s and had a brief period of popularity during World War II when there was a lack of oil. This is not a novel concept, nor is it really a new kind of technology. On the other hand, fossil fuels turned out to be less expensive and simpler to deal with.
Since ammonia burns more slowly than fossil fuels and requires more effort to ignite, the majority of ammonia engines need a boost of diesel or hydrogen in order to begin going. Leaking unburned ammonia from engines is a potentially dangerous occurrence. In addition, ammonia engines have a propensity for producing nitrogen oxide, which is another powerful greenhouse gas. However, there are devices known as catalytic converters that may rectify this issue. Faria believes that environmentally friendly engines driven by ammonia are within reach. “We’re talking about smoothing out the kinks in something that’s already very developed,” you say. “That’s right.”
Major engine manufacturers such as the German MAN Energy Solution and the Swiss WinGD are currently developing ammonia-fueled engines as well as kits to retrofit older engines so that they can run on ammonia. The first products developed by these manufacturers are anticipated to be installed on ships in 2024. In the meantime, new businesses are entering the fray as well. William Northrop, a colleague of Reese’s, established Aza Power Systems in Minnesota a month ago with the intention of commercializing the company’s proprietary ammonia-powered engine technology.
Ammonia-powered turbines for the generation of electricity are also being developed by firms that focus on the production of power. You only get approximately 20 to 30 percent of the power back at the end, adds Faria, compared to, for example, the 98 percent efficiency of a battery. This would sound absurd: use electricity to produce hydrogen, use that to make ammonia, transfer the ammonia, then transform it back into electricity again. However, he believes that the advantages of conveniently storing and transmitting that energy outweigh the disadvantages of doing so.
Conclusion
The green ammonia industry is anticipated to rapidly expand regardless of the exact path that events take, according to market watchers. According to research such as that conducted by the IEA, ammonia, in addition to biofuels and hydrogen, will have a part to play in the process of getting to a point when there will be no net emissions of greenhouse gases. As the cost of carbon rises, green ammonia will emerge as the market leader.
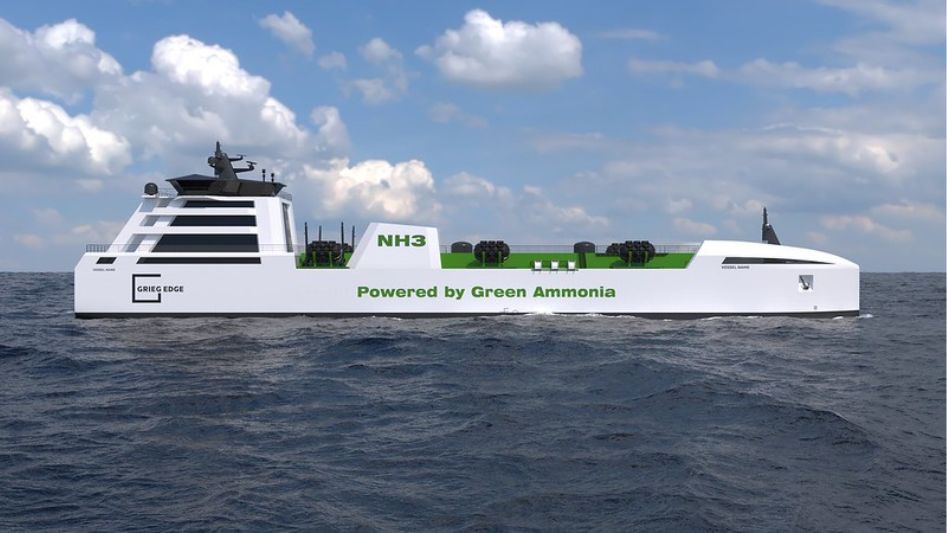
FAQ
Does ammonia contribute to climate change?
According to some estimates, the production of ammonia is responsible for approximately 2% of the use of fossil fuels worldwide. Additionally, the production of ammonia results in the release of more than 400 million tons of CO2, which is equivalent to more than 1% of the total annual global emissions of the greenhouse gas.
Is the use of ammonia harmful to the environment?
The molecules that make up ammonia (NH3) have one component of nitrogen and three components of hydrogen. NH3 is a viable and ecologically benign fuel source due to the fact that it does not include any carbon, it contains 1.5 times more hydrogen than liquid hydrogen (H2), and it has the potential to significantly cut global GHG emissions by replacing fossil fuels.
What are some applications for green ammonia?
According to Dolan, the most straightforward solution would be to utilize green ammonia as a fertilizer in the same way that ammonia is used now, but without incurring the associated carbon cost. Beyond that, ammonia may be transformed into energy in a power plant that is specifically designed to burn ammonia, or it could be done in a conventional fuel cell, which is what the South Australia facility proposes to accomplish.
Is it possible to maintain green ammonia?
Ammonia is a gas that has a strong odor and is often utilized in the production of agricultural fertilizers. Producing ammonia in a manner that is both 100 percent renewable and free of carbon emissions is referred to as “green” ammonia production.
You May Also Like
- THE NEW HYDROGEN PRODUCTION METHOD NO-ONE IS TALKING ABOUT
- SMALL WIND TURBINES HOW DO THEY WORK:
- NEW DATA SOUND GOOD FOR WIND ENERGY NICHOLAS
- ACTIONS TO ACHIEVE NET-ZERO EMISSIONS IN HONG KONG
- HOW TO INTEGRATE ENVIRONMENTAL SUSTAINABILITY INTO YOUR BUSINESS STRATEGY?
External Links
- Green ammonia could produce climate-friendly ways to store energy and fertilize farms
- Ammonia—a renewable fuel made from sun, air, and water—could power the globe without carbon
- From Fertilizer to Fuel: Can ‘Green’ Ammonia Be a Climate Fix?
- The potential of green ammonia for our climate
- $4.6 billion plant in South Africa will make ‘the fuel of the future’